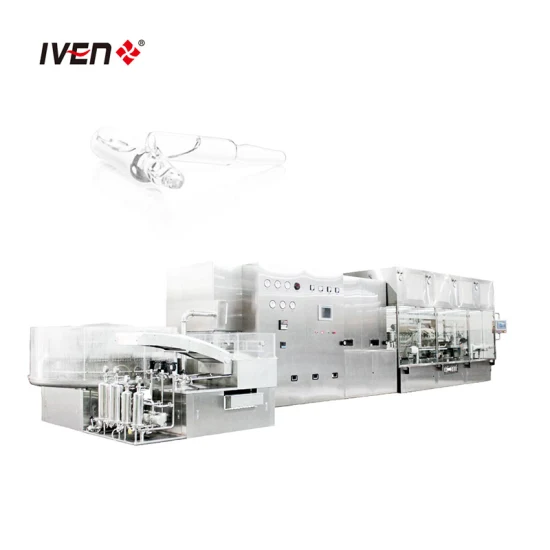
Injectable Glass Plastic Ampoule Filling and Sealing Machine Production Line
Description
Basic Info.
Condition | New |
Warranty | 1 Year |
After-sales Service | Field Installation, Commissioning and Training |
Capacity | Standard/Customized; |
Applicable Bottle | 1-30ml Glass Vial Bottle |
Optional Configuration | Inspection, Labeling, Blistering, Cartoning |
Process Type | Washing, Sterilizing, Filling, Stoppering, Capping |
Filling Capacity | 100-600bpm |
Transport Package | Wooden Package |
Specification | 2500*2500*1300 mm - 4280*1650*2400 mm |
Trademark | IVEN |
Origin | China |
HS Code | 8422303090 |
Production Capacity | 7000~10000 PCS/H |
Product Description
1, 2, 5, 10, 15, 20, 30 ml Injectable Glass Plastic Ampoule Filling and Sealing Machine
The Ampoule filling production line includes vertical ultrasonic washing machine, RSM sterilizing drying machine and AGF filling and sealing The Ampoule SVP Injectable Liquid Filling Production Line includes Ultrasonic washing machine, Sterilizing tunnel, Ampoule filling and sealing machine. Its divided into washing zone, sterilizing zone, filling and sealing zone. This compact line can work together as well as independently. Compared with other manufacturers, our equipment has unique features, including overall dimension smaller, higher automation & stability, lower fault rate and maintenance cost, and etc. Product Advantages1. The compact line realizes single linkage, continuous operation from washing, sterilizing,filling and sealing. The whole production process realizes cleaning operation; protects products from contamination, meets the GMP production standard.
2. This line adopts water and compressed air cross pressure jet wash and ultrasonic wash at inverted state. The cleaning effect is very good.
3. The ultra filtration technology is applied at the washing machine's filter. The clean and sterile washing water and compressed air is obtained through terminal filter, which can improve the clarity of the washed bottle.
4. Bottle in feed auger and star wheel meet, the auger space is small. Ampoule can walk straight. Ampoule can transfer more stable and can hardly broken.
5. The stainless manipulators are one side fix. The location is more accuracy. The manipulators are wear proof. When changing of pitch the manipulators no need stretch out and turn. The turning bearing wont contaminating the cleaning water.
6. The ampoule are sterilized by the hot air laminar flow sterilization principle. The heat distribution is more even. The ampoule are under the HDC high temperature sterilization condition, which meets the standard of GMP.
7. This equipment adopts negative pressure sealing principle to seal the high efficiency filter which are used for purify the tunnel. The filter is easy to install which can ensure the one hundred purification condition.
8. The equipment adopts hinge type seat heat and horizontal hot air fan structure. The maintenance of the equipment is more convenient and laborsaving.
9. This equipment adopts chain conveying belt with flank. The conveying belt won't be off track, anti-creeper, no bottle falling.
10. The equipment adopts advance technology such as mufti-needle filling, front and rear nitrogen charging and wire drawing sealing, which can meet the standard of different type of products.
11. The fill-seal machine adopts balcony structure. The star wheel in feed and convey bottles continuously, the running of the equipment is stable and less bottle breakage.
12. This equipment is universal. It can't be used to 1-20ml ampoule. Changing parts are convenient. In the meantime, the equipment can be used as vial washing, filling and capping compact line by changing some mould and out feed wheel.
Production Procedures:
Step 1
Ultrasonic washing
It adopts washing technology of 2 water and 2 air on the outer wall and 3 water and 4 air on the inner wall.
6 groups of spraying needles have track washing, spray needles adopts full 316L stainless steel. Servo control system+ Guide sleeve and guide board give accurate position to the spray needle, effectively avoid needle damage caused by mismatch.
WFI and compressed air is intermittent, reduce the consumption.
Standard washing process:
1.Bottle spraying
2.Ultrasonic pre-washing
3.Recycled water: inside washing, outside washing
4.Compressed air: inside blowing
5.Recycled water: inside washing, outside washing
6.Compressed air: inside blowing
7.WFI: inside washing
8.Compressed air: inside blowing, outside blowing
9.Compressed air: inside blowing, outside blowing
Step 2
Sterilizing& Drying
The washed bottles enter into sterilizing &drying machine slowly uniformly through mesh belt. Pass through preheating zone, high temperature sterilizing zone, cooling zone gradually.
The moisture exhausting fan discharge the bottle vapor to outdoor, in high temperature zone, the bottles are sterilized about 5 minutes under 300-320ºC. The cooling zone cools the sterilized vials, and finally reach to technological requirement.
The whole drying and sterilizing process is operated under real time monitoring.
Step 3
Filling& Sealing
This machine adopts a transmission system of step-by-step with balcony structure.
The machine automatically finishes the whole production process:
Auger conveying---Front nitrogen charging (optional)---Solution filling---Rear nitrogen charging (optional)--- Preheating---Sealing---Counting---Finished products outputting.
Ampoule Filling Production Line Advantages
1. The compact line realizes single linkage, continuous operation from washing, sterilizing,filling and sealing. The whole production process realizes cleaning operation; protects products from contamination, meets the GMP production standard.
2. This line adopts water and compressed air cross pressure jet wash and ultrasonic wash at inverted state. The cleaning effect is very good.
3. The ultra filtration technology is applied at the washing machine's filter. The clean and sterile washing water and compressed air is obtained through terminal filter, which can improve the clarity of the washed bottle.
4. Bottle in feed auger and star wheel meet, the auger space is small. Ampoule can walk straight. Ampoule can transfer more stable and can hardly broken.
5. The stainless manipulators are one side fix. The location is more accuracy. The manipulators are wear proof. When changing of pitch the manipulators no need stretch out and turn. The turning bearing wont contaminating the cleaning water.
6. The ampoule are sterilized by the hot air laminar flow sterilization principle. The heat distribution is more even. The ampoule are under the HDC high temperature sterilization condition, which meets the standard of GMP.
7. This equipment adopts negative pressure sealing principle to seal the high efficiency filter which are used for purify the tunnel. The filter is easy to install which can ensure the one hundred purification condition.
8. The equipment adopts hinge type seat heat and horizontal hot air fan structure. The maintenance of the equipment is more convenient and laborsaving.
9. This equipment adopts chain conveying belt with flank. The conveying belt won't be off track, anti-creeper, no bottle falling.
10. The equipment adopts advance technology such as mufti-needle filling, front and rear nitrogen charging and wire drawing sealing, which can meet the standard of different type of products.
11. The fill-seal machine adopts balcony structure. The star wheel in feed and convey bottles continuously, the running of the equipment is stable and less bottle breakage.
12. This equipment is universal. It can't be used to 1-20ml ampoule. Changing parts are convenient. In the meantime, the equipment can be used as vial washing, filling and capping compact line by changing some mould and out feed wheel.
Tech Parameters
We've already exported to more than 45+ countries in Aisa, Europe, Middle East, Africa, South America,etc.
2. Can you arrange the visit to your user?
Yes. We can invite you to visit our turnkey projects in Indonesia, Vietnam, Uzbekistan, Tanzania etc.
3. Can you customize the machine according to our requirements?
Yes.
4. Is your equipment in accordance with GMP, FDA, WHO?
Yes, we will design and manufacture the equipment according to the requirement of GMP/FDA/WHO in your country.
5. What is your payment terms?
Generally, TT or irrevocable L/C at sight.
6. How about your after-sales service?
We will reply you within 24 hours by email or phone.
If we have local agent, we will arrange him to your site within 24 hours to assist you to shoot the problem.
7. How about the staff training?
Normally, we will train your staffs during the installation in your site; you are also welcome to send your staff train in our factory.
8. How many coutries have you done the Turnkey Project?
Russia, Nigeria, Tanzania, Ethiopia, Saudi Arabia , Uzbekistan, Tajikistan, Indonesia, Vietnam, Thailand, Myanmar etc.
9. How long will the turnkey project take?
About 1 year from designing the layout to finish installation and commissioning.
10. Which kind of after-sales service you can offer?
Except the regular service, we can also provide you know-how transfer, and dispatch our qualified engineers to help you run the factory up to 6-12 months.
11. What should we prepare for setting up IV plant basically?
Please prepare the land, building construction, water, electricity, etc.
12. What kind of certificate you have?
We have ISO, CE certificate, etc.
Our Contact